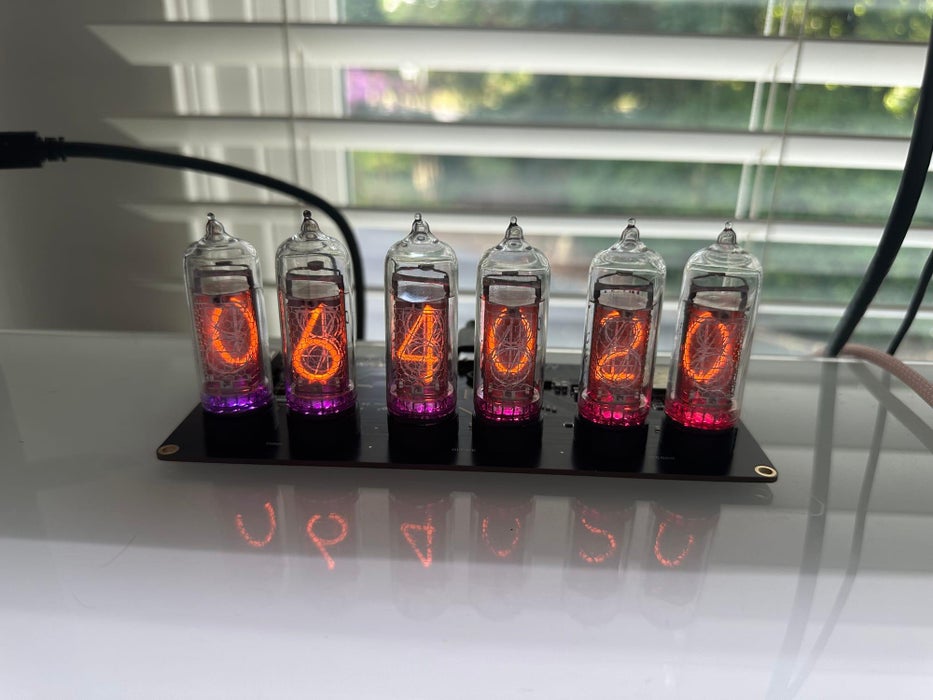
Hey! I’m a student at Purdue University studying computer science and I’ve always wanted to make my own Nixie tube clock. Nixie tubes were extremely popular in the 50s and 60s and were the precursor to LED and VFD displays. I love the idea of driving old and forgotten technology with modern components.
I submitted this to the Colors of the Rainbow contest as it uses the natural orange glow of the Nixie tubes as the centerpiece. It also allows the full spectrum of colors to be put on display by using the full-color LEDs underneath the tubes!
But, I forgot about the idea for a few years until I was scrolling through eBay and found a set of six NOS (new, old-stock) IN-14 Nixie tubes for $99. I couldn’t pass these up, so I bought them and immediately started brainstorming how to use them.
Supplies
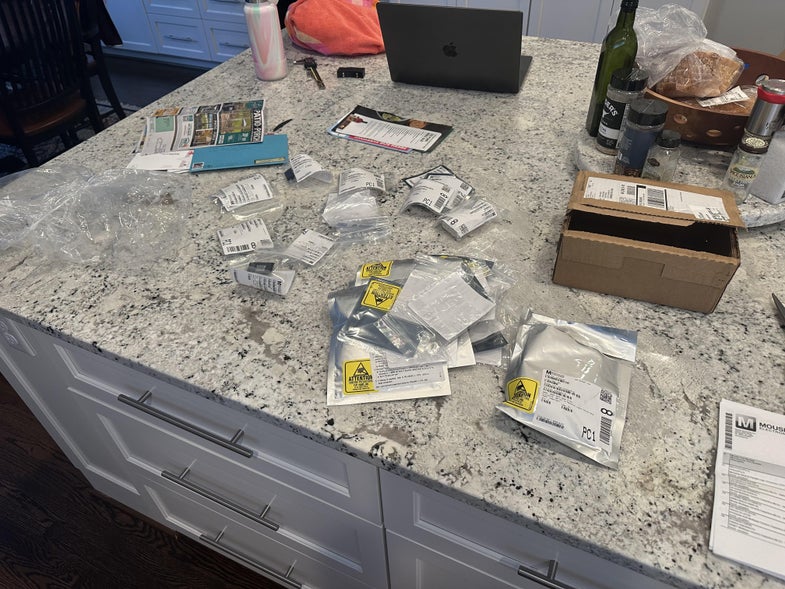
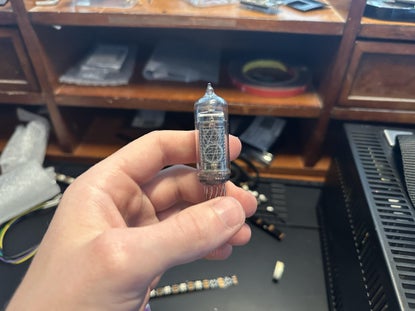
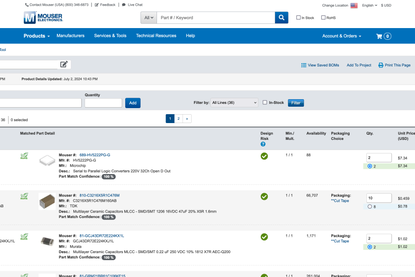
You’ll need to order the components listed in the BOM file available on the design repository here:
https://github.com/acvigue/esphome-nixie2
The easiest way to get this done is to use the BOM import tool on either Mouser or DigiKey.
You’ll also need access to one of the following: (in order of preference)
- reflow oven
- hot air rework station,
- hot air gun
For assembling the PCB:
- solder paste
- credit card
You will also need access to a 3D Printer
The PCB can be ordered using the Gerber files also available in the design repository. These can be uploaded on JLCPCB’s website! When ordering the PCB, also order a single sided stencil.
You’ll also need six IN-14 tubes, these are available on eBay. Preferably, buy ones that are marked NOS (new, old-stock) as these will last the longest.
Step 1: Design PCB
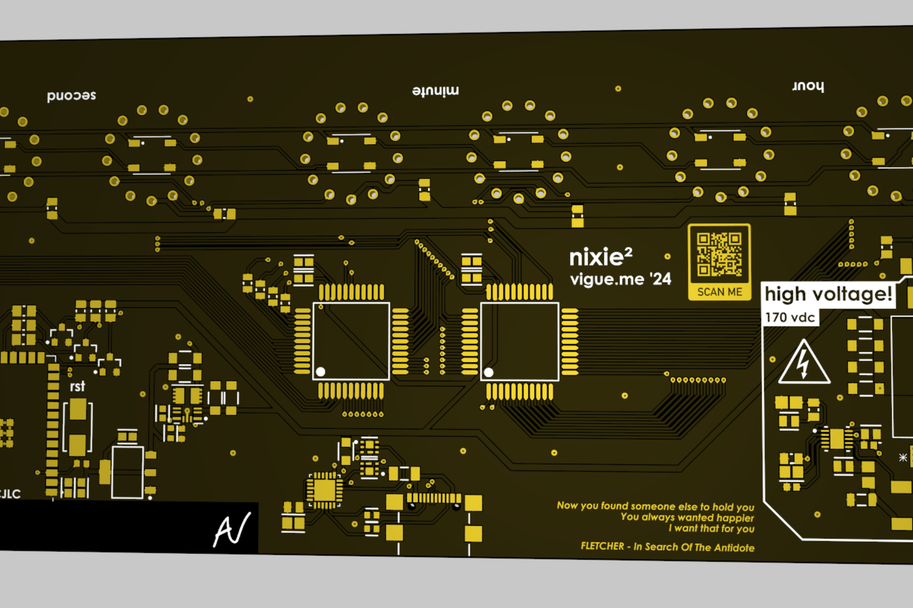
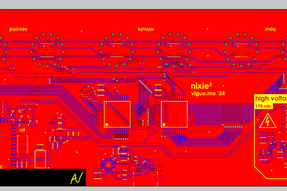
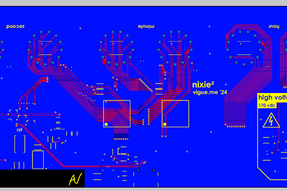
This is already done, but if you’d like to make edits, here’s how.
You can download the student version of Altium Designer from their website and edit the provided project files to make modifications to the board.
A few suggestions are to add RGB underlighting or to add more digits for the date!
Personally, I started the design process by creating the schematics that I was going to base the circuit board off of. I used Altium’s KiCAD import tool to import the footprint for the IN-14s from a library I found online.
The 15V to 5V/3.3V stepdown is controlled by a TPSM33625 buck converter paired with a bog-standard LDO regulator.
I wouldn’t modify the 15V to 170V step-up converter as it’s been optimized for efficiency.
If you don’t want to use USB-C power delivery, you can build “Revision B” of the circuit board, also available in the design repository. I’ve attached a few photos of schematic prints for reference!
Step 2: Order PCB

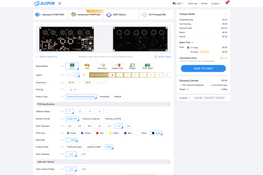
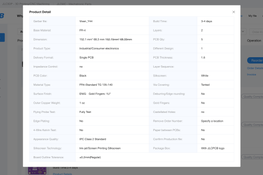
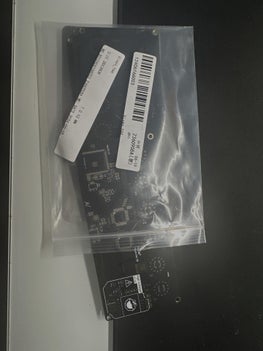
Being able to design a circuit board on the computer and have it in your hands in less than a week is insane! I ordered my PCBs from JLCPCB as they have excellent quality while remaining extremely fast and inexpensive.
I went to JLCPCB.com and uploaded the Gerber board files. Then, I selected a black solder mask with ENIG (gold) finish. I also ordered a solder stencil with a customized size to keep shipping costs low (170x80mm).
They took around 3 days to manufacture and were shipped internationally via DHL and showed up two days later in a heavy-duty plastic bag that I like to use to keep my project materials separate.
Here is a direct link to the order form. There’s also a coupon on there that may help to bring the cost down!
Step 3: Assemble PCB
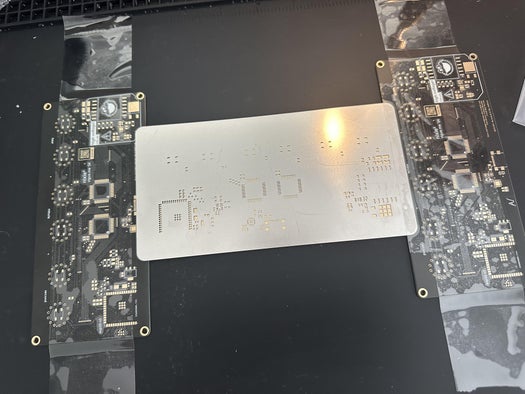
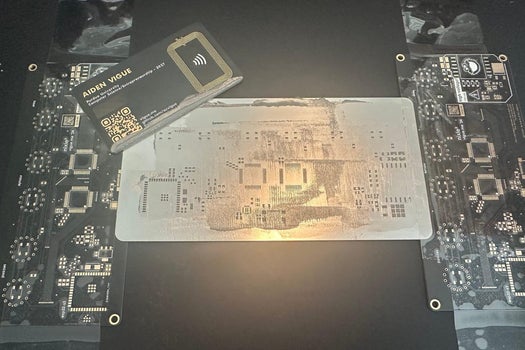
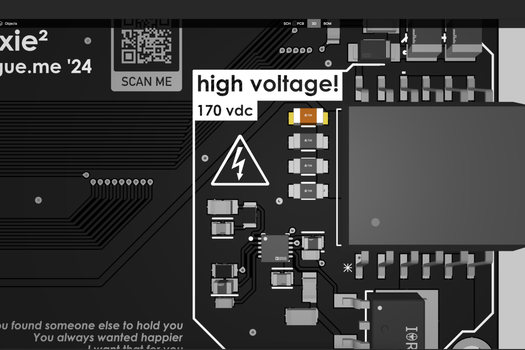
Use the stencil and credit card to squeegee solder paste along the top of the board.
You can follow the BOM placement guide to help you align components to the proper locations on the board!
The placement guide is linked in the design repository
Step 4: Reflow Board
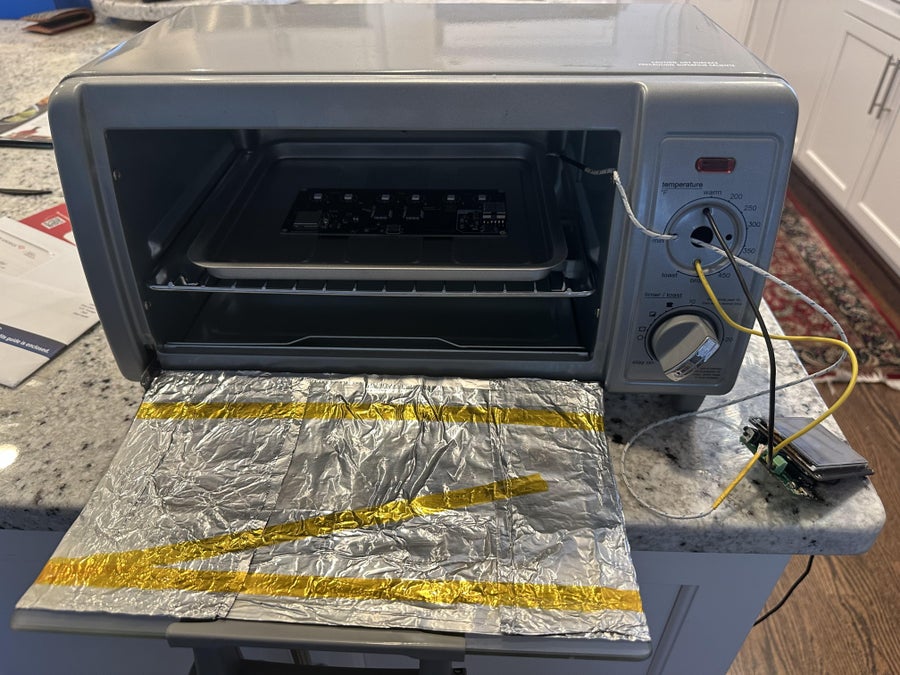
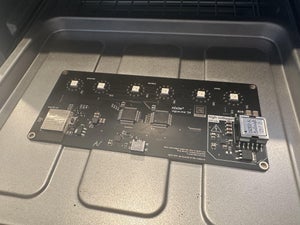
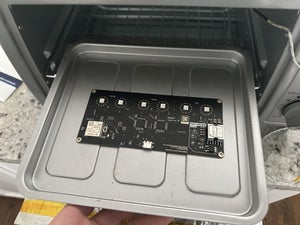
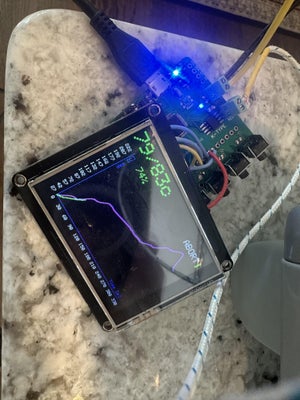
Then, use the reflow oven or hot air rework station to melt the solder paste. This will secure the components on the board.
Personally, I use a Target reflow oven with the Reflow Master control board.
Step 5: Examine Board
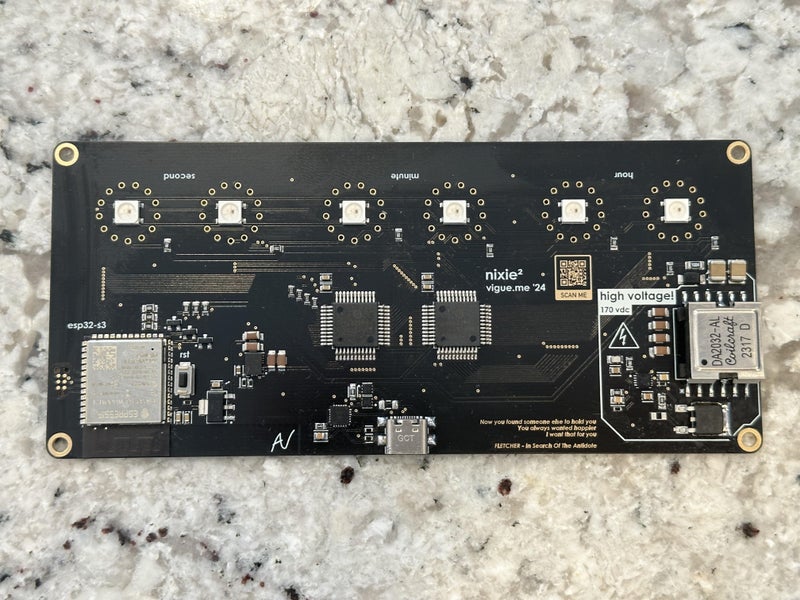
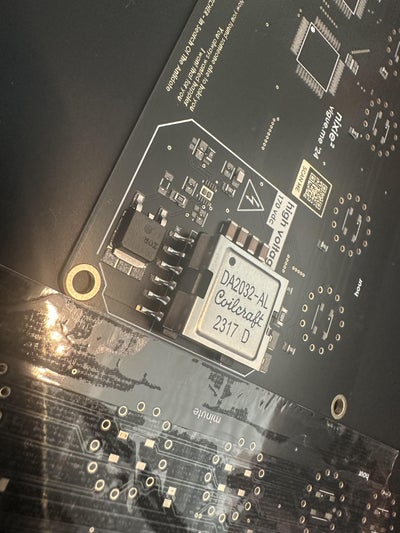
While this step is optional, I highly recommend examining the different sections of the board to ensure that all the components are properly soldered and that there aren’t any bridges.
Step 6: Solder on Tubes
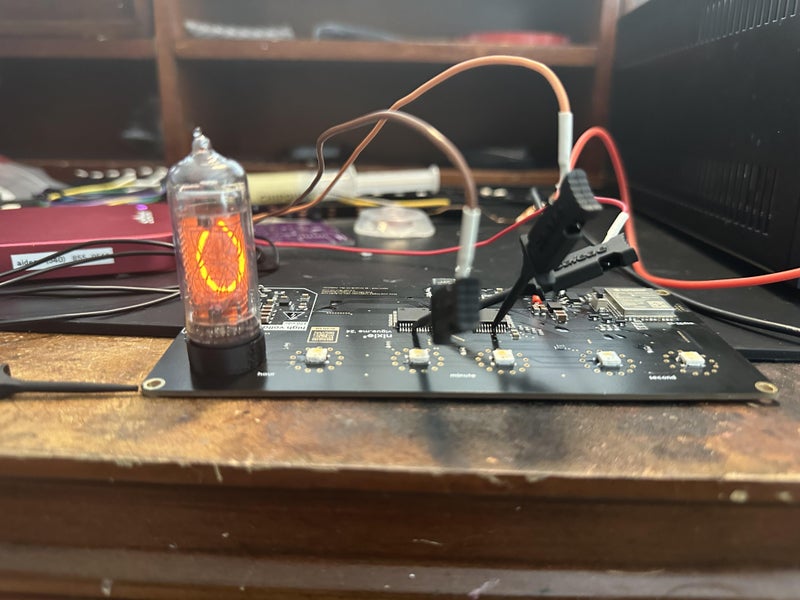
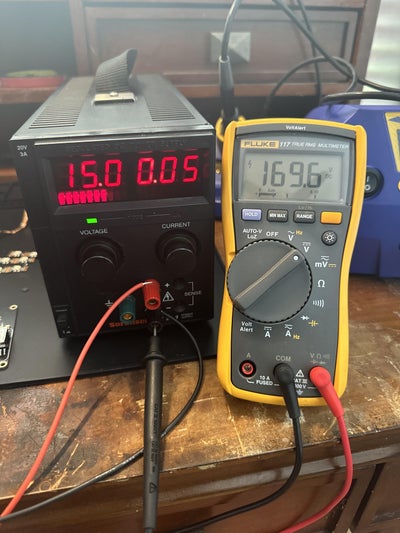
This step may be different depending on the exact tubes you purchased.
I printed 6 of these spacers in black ABS plastic. They have cutouts to allow the LEDs underneath to shine onto the Nixie tubes.
There’s an arrow on the bottom of each tube pointing to a pin. That pin should be the one furthest from the front.
Step 7: Program PCB
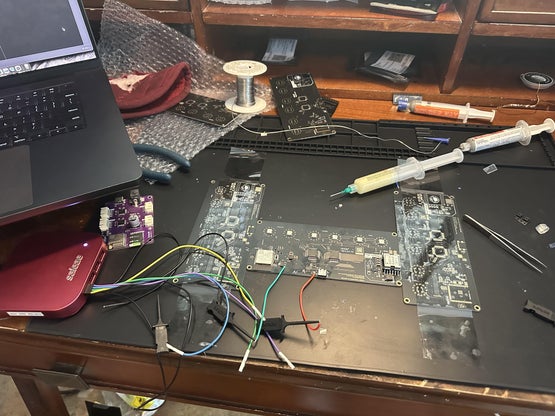
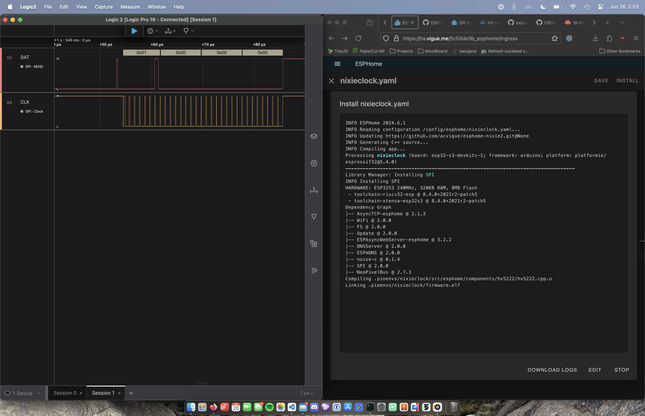
(I programmed mine before soldering on the tubes as I didn’t want to blow them up because I didn’t know how the driver chips worked)
I used ESPHome to write the firmware to install on the board! You can simply copy and paste the example configuration file into a new ESPHome document. It will automatically download the custom code that I wrote to drive the tubes. Make sure you change the Wi-Fi credentials though!
Step 8: Enjoy!
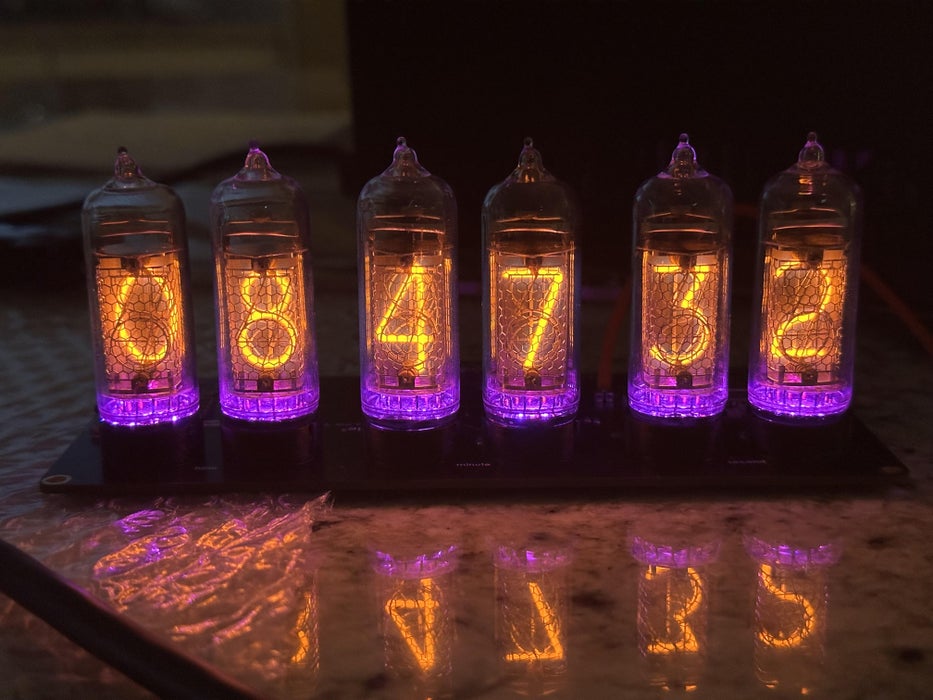
Enjoy your new Nixie clock. My next steps are to design and fabricate a cover out of clear acrylic.